Preventative HVAC maintenance is essential to maintaining the efficiency and longevity of your heating, ventilation, and air conditioning system.
Regular maintenance ensures that your HVAC system is functioning at its best, providing you with a comfortable indoor environment and reducing the likelihood of costly repairs. Motili is a leading provider of preventative HVAC maintenance services, helping homeowners and businesses keep their systems in top condition.
In this article, we will explore the benefits of preventative HVAC maintenance and how it can help improve the performance and lifespan of your HVAC system. We will also discuss the services offered by Motili and why they are the best choice for your preventative HVAC maintenance needs.
Whether a homeowner or a businesas owner, taking the necessary steps to maintain your HVAC system is essential to ensure its longevity and efficiency. Get started with Motili today and enjoy the peace of mind that comes with knowing your HVAC system is in good hands.
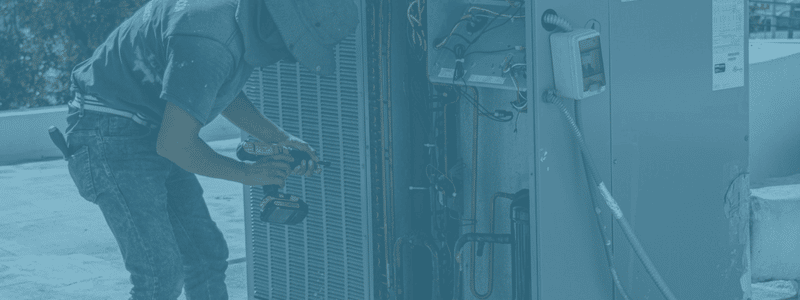
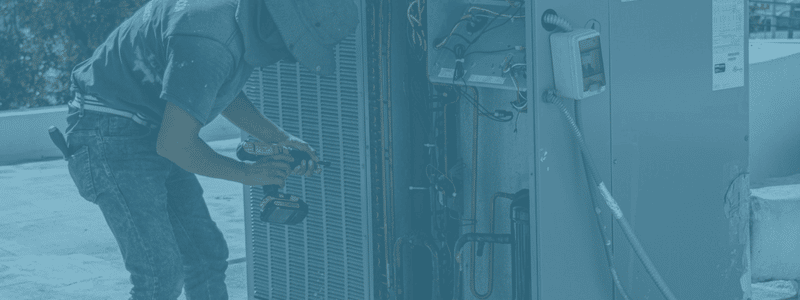
For multi-family and commercial building owners and operators, malfunctioning HVAC systems lead to lost revenue.
Whether it’s through decreased resident satisfaction, spoiled product, increasing energy bills, or expensive repairs, improperly installed, outdated, or broken HVAC systems reduce energy efficiency between 10% – 35%.
Regular preventative maintenance can keep HVAC systems in optimal efficiency and operating condition, reducing expenses not only for reactive maintenance and repairs but also through increased efficiency.
Preventative maintenance can produce millions in savings every year for companies managing hundreds or thousands of units across a portfolio.
What is Preventative Maintenance?
Preventative maintenance is a proactive approach to prevent or limit potential malfunctions by conducting more straightforward tasks and repairs ahead of a breakdown.
A preventive approach is essential for keeping an HVAC system in optimum working order for a variety of reasons, including:
- Broken or worn parts can be identified before they cause a severe malfunction
- System performance can be optimized, improving energy efficiency
- Internal components can be cleaned, so they don’t negatively affect indoor air quality
- The overall life of the system is extended, increasing its lifetime return on investment
- Fire hazards and any other safety concerns can be addressed and corrected before an accident occurs
- Clean equipment improves a residential property’s curbside appearance.
Despite these benefits, many property owners and managers must perform regular preventative maintenance on their HVAC systems. As a result, the costs might not be included in their budgets, or it might be challenging to measure the direct cost advantages when a system is operating efficiently.
In larger multi-family and commercial buildings, owners and operators may need to determine if all or most of their systems are functional.
“If it ain’t broke, why fix it?” It’s easier to prioritize other expenditures in the here and now than to proactively allocate resources toward preventing a hypothetical, yet-actually-very-real, future issue. Besides, how do you measure a system’s extended or limited lifetime if you still determine what it would have been otherwise?
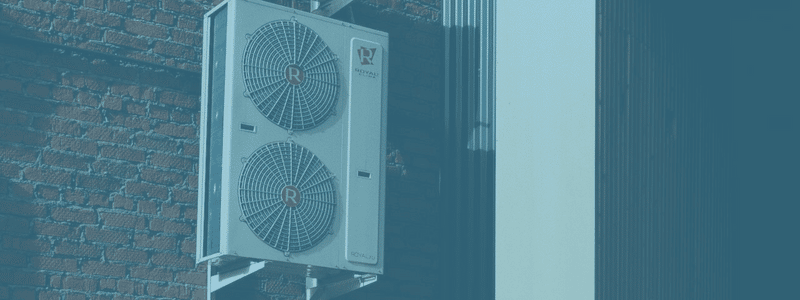
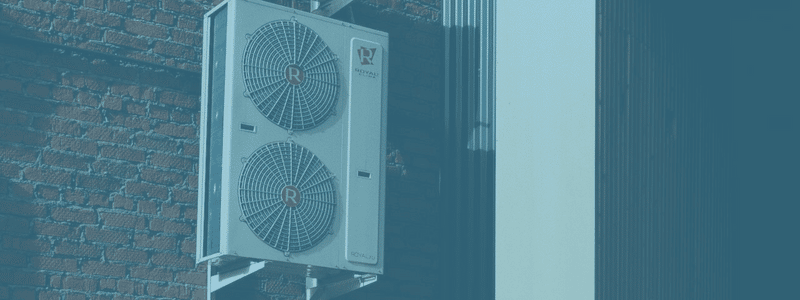
An Ounce of Prevention is Worth a Pound of Cure
Preventative HVAC maintenance may appear to some to lack an obvious ROI, but studies have proven otherwise.
When researchers from Jones Lang LaSalle analyzed the costs of regular preventative maintenance compared to savings resulting from it, they found an astounding 545% ROI.
To help determine the value of preventative HVAC maintenance, the JLL team examined 14 million square feet of mixed property types and identified the actual cost of preventive maintenance and the costs of repair or corrective maintenance, including replacement parts and equipment.
They then considered the expected operational lifetime of equipment, the effects preventative maintenance had on the expected lifetime, the frequency of necessary repairs on unmaintained equipment, and the effect the preventative maintenance had on energy consumption.
Based on the analysis of the collected data, the researchers determined that the cost of preventative maintenance is almost always justified.
The study found that a $32,000 compressor might last 16 years without preventative maintenance. Still, its lifetime can be extended to 20 years with it.
Without maintenance, the equipment will need repair every three years at an average cost of $944 per incident. Preventative maintenance on the system, on the other hand, costs $472 per year and extends the length between repairs to once every four years.
What’s the Take-Away?
With preventative maintenance, the repair costs on a system will average $236 per year, compared to an average of $315 per year without it.
Plus, an unmaintained compressor will need to be replaced four years earlier, which decreases the initial investment of the unit from $2,000 per year for its lifetime to just $1,600 per year until it needs to be replaced – a difference that practically pays for the preventative maintenance by itself.
The additional cost reductions increase the ROI of regular maintenance – on a single piece of equipment!
“The longer the capital expense can be delayed, the higher the ROI,” study authors Wei Lin Koo and Tracy Van Hoy wrote in their analysis. “Maintaining all the equipment in the portfolio produces the significant returns identified by the analysis and offers a powerful argument for the value of preventive maintenance and the dramatic impact PM [preventative maintenance] can have on real estate investments.”
If It Ain’t Broke, Don’t Fix It?
Of course, keeping up with a regular maintenance schedule is easier said than done. But it’s not as though property managers and facility managers need more on their plates already.
Besides, regular preventive HVAC maintenance is only effective if it’s… well… regular. Fortunately, there’s a technology that addresses this need.
Preventative maintenance technology takes the guesswork out of managing HVAC and hot water assets. Various tools, including Motili’s HVAC and hot water management technology, can schedule preventative maintenance and track equipment, notifying the property owner or facility manager when equipment is due for replacement. In an expanding range of applications, the technology can even monitor efficiencies and analyze potential problems before a malfunction occurs.
The Environmental Impact of Preventative HVAC Maintenance
In today’s environmentally conscious world, the significance of reducing our carbon footprint is paramount. Preventative HVAC maintenance plays a crucial role in this endeavor. Regular maintenance of heating, ventilation, and air conditioning systems is not just about ensuring comfort or prolonging equipment life; it’s also about nurturing a sustainable environment.
Reducing Energy Consumption: One of the most immediate benefits of preventative HVAC maintenance is the reduction in energy consumption. Well-maintained systems operate more efficiently, consuming less power to achieve desired heating or cooling levels. This efficiency translates directly into lower energy usage, which not only saves money but also decreases the environmental impact associated with energy production.
Lowering Greenhouse Gas Emissions: As HVAC systems become more efficient through regular maintenance, their emissions are reduced. Older or poorly maintained systems often work harder, leading to higher greenhouse gas emissions. By keeping these systems in optimal condition, we can significantly cut down on the harmful gases released into the atmosphere.
Improving Air Quality: Preventative HVAC maintenance includes cleaning and replacing air filters and inspecting ductwork for leaks or blockages. This not only ensures efficient operation but also directly impacts the indoor air quality. By maintaining clean air filters and ducts, the system can better eliminate pollutants and allergens from the air, contributing to a healthier indoor environment and reducing the overall environmental impact.
Promoting Longevity and Reducing Waste: Regular maintenance extends the life of HVAC units, which means fewer units end up in landfills. The manufacturing of HVAC units is resource-intensive, involving metals, plastics, and chemicals. By extending the life of these systems, preventative maintenance reduces the need for new units, thereby saving resources and minimizing waste.
Encouraging Sustainable Practices: Incorporating preventative HVAC maintenance into building management practices promotes a culture of sustainability. It sets a precedent for other areas of environmental concern, such as water conservation and waste management, establishing a holistic approach to a greener future.
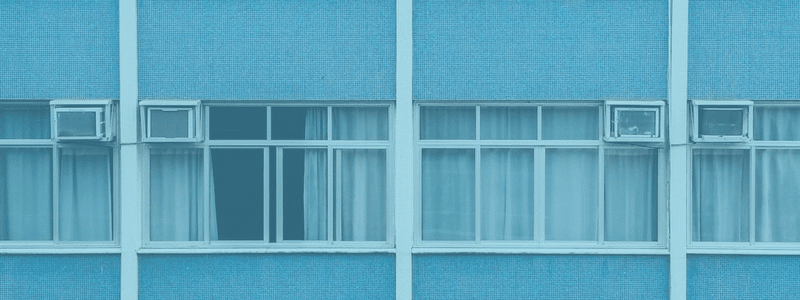
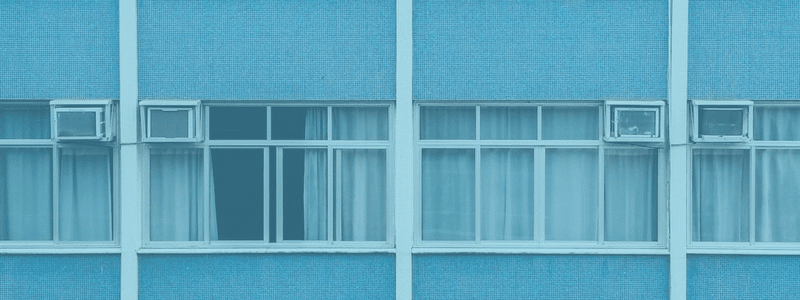
Motili HVAC Preventive Maintenance
Motili is more than mere asset management, it offers a nationwide network of 2,000+ contractors, saving property owners money. Other platforms might offer a list of service providers, but Motili connects property managers directly to contractors.
Motili’s contractor network is fully plugged into the Motili desktop and mobile app for contractors, which technicians utilize to manage every job from start to finish. Keeping everything in the app allows Motili to have tight control over data, photos, records, etc… which are then available perpetually in one place.
Motili’s asset and data management technology keeps track of all asset-tagged HVAC equipment, cataloging it and creating a multi-year HVAC asset plan. In addition, Motili continually analyzes the data collected from users’ properties, assets, and jobs ordered through the platform. That way, the data can be aggregated to track performance and predict future needs.
Motili provides its customers with ongoing support for all planned repair and replacement jobs so that they can focus their precious time on a long list of other tasks. However, even if a property manager finds plenty of time to schedule preventative maintenance, they will need more comprehensive data.
FAQ – Preventative HVAC Maintenance
Q: What is Preventative HVAC Maintenance?
A: Preventative HVAC maintenance involves regular inspections and servicing of your heating, ventilation, and air conditioning system to ensure it operates efficiently. This proactive approach helps in identifying and fixing minor issues before they turn into major problems.
Q: How Often Should HVAC Systems Be Serviced?
A: It’s generally recommended to service your HVAC system at least once a year. However, specific servicing frequencies can vary based on the type of system, its age, usage patterns, and manufacturer recommendations.
Q: What Are the Benefits of Regular HVAC Maintenance?
A: Regular maintenance extends the lifespan of your system, improves energy efficiency, ensures consistent comfort levels, prevents unexpected breakdowns, and can save you money on costly repairs.
Q: Can I Perform HVAC Maintenance Myself?
A: While basic maintenance like changing filters can be done by homeowners, more complex tasks should be handled by professionals. This is to ensure the system is properly inspected and serviced without risking damage or voiding warranties.
Q: What Does Professional HVAC Maintenance Include?
A: Professional maintenance typically includes cleaning air ducts, checking and refilling refrigerant levels, inspecting electrical components, testing thermostat functionality, and ensuring all parts are in good working order.